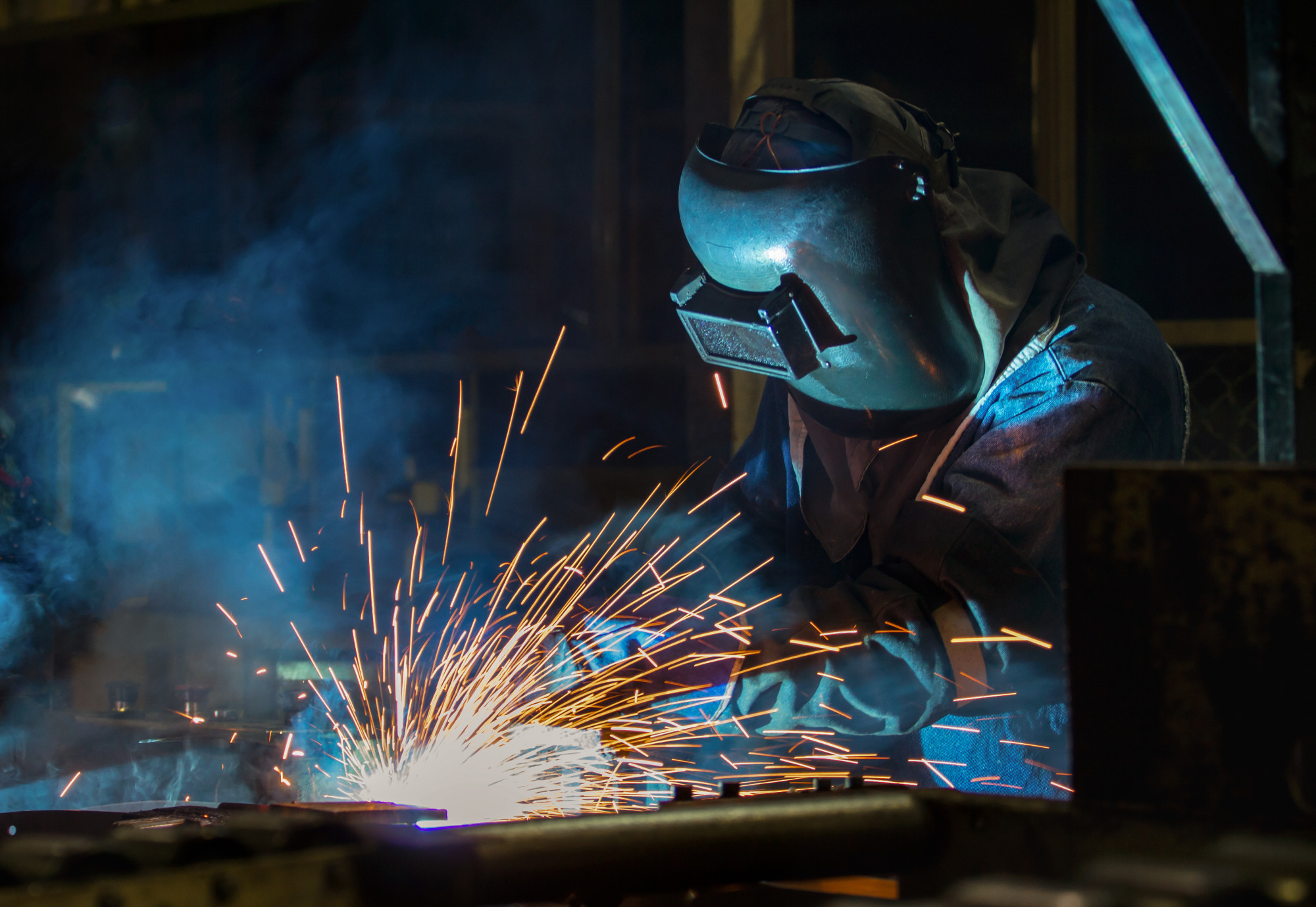
The 4 Welding Types That Every Welder Should Know About
According to the Bureau of Labor Statistics, a welder earned on average $41,380 per year in 2018. With most Americans focusing on white-collar jobs, there are numerous possibilities and opportunities for budding welders. The United States’ economy looks up to Americans in the blue-collar sectors to steer growth considering the demand for technical skills.
Are you looking to pursue and excel in a career in welding? It would help if you were well-versed with the dynamics in the career. To start you off, here are four of the leading welding types you ought to be aware of before kick-starting your career path. Read on to get more information on the various welding types.
Contents
1. Shielded Metal Arc Welding
The shielded metal arc welding technique is the oldest and perhaps the most common approach to arc welding. Welding was a common practice as early as the 1890s. With this method, you’ll learn how to use electricity charge that transcends through the coated electrode then touches the base of the metal.
In this approach, the arc is sustained after the electrode is withdrawn. This allows the heat to melt the coating. The melting coat becomes a shielding gas. With the remainder of the metal melting into the weld pool, the process ends with the solidification of the alloys.
For most beginners, this process may appear complicated and hard to actualize. But once you engage the practical application, shielding metal arc welding is perhaps the most straightforward form of metalwork.
Uses
The technique of shielded arc welding is useful in many sectors and fields. If you are looking for an option that will ensure your marketability. Then your eyes should be set on the opportunities in the pipeline, construction, and shipbuilding sectors. For most technicians hoping to venture into the farm machinery and underwater welding options, they can also benefit significantly from a course in shielded arc welding.
The Pros of Working as a Shielded Metal Arc Welder
Well, of course, apart from the fact that you’ll get to earn a living. Shielded metal arc welding also presents other benefits. For instance, considering the equipment used is portable, you never have to worry about transportation to the specific sites or the need for storage space for the welding equipment. This welding method is useful when completing welding on a range of metal types.
Such an advantage makes it possible to use shielded metal arc welding across a diverse range of projects. The method is best used outdoors, which enhances the aspect of safety for the welder.
2. Gas Metal Arc Welding is among the Common Welding Types
Opting for the GMAW method exposes you to the use of shielding gas as opposed to electricity in the course of welding. In this option, the electrode used is a metal wire that passes through a welding gun. The shielding gas heats the two metals tips to be joined, which requires constant high voltage heat.
You’ll learn how to join two different metals during this process of welding using four primary approaches to metal transfer. The methods include globular, short-circuiting, the spray method, and the pulsed-spray technique. Under the GMAW, there are two subgroups, namely, Metal Inert Gas and the Metal Active Gas welding option.
Uses
Gas metal arc welding is useful across a range of industries. If you pursue this option, you’ll have the skills to undertake automotive production and maintenance. You’ll also thrive in the manufacturing and the railroad track installation and maintenance process.
Such opportunities are an indication of the broad-range of welder careers you can consider. Other common uses of gas arc welding include pipe joining and underwater welding.
Advantages
Compared to other options, the gas-metal arc welding option is cost-effective. Further, this approach is fast, which makes it useful in the long-term. Compared to other options, the Gas Metal Arc welding method minimizes waste, which makes the approach environmentally friendly.
3. Flux- Cored Arc Welding
Flux-cored welding was introduced as an alternative to the shield welding approach. The technique is among the few welding types which uses a machine, which feeds electrodes into the weld joints. Using the flux-cored arc welding approach eliminates the risk of atmospheric contamination.
The technique is semi-automatic or automatic by design. But there’s a need to have a continuously-fed electrode containing a flux to ensure efficiency. Flux-core welding offers a high deposition rate. The “all position” process is among the most common welding methods in use today.
If you are looking for an in-demand welding career path, then the flux-cored wire welding course is worth your time. As opposed to other forms of welding, the flux-cored will not blow off easily. The approach gives you a clean welding process making it one of the techniques with uncontaminated outcomes.
Advantages and Uses
The most common applications of flux-cored welding are in pipeline welding. You may also utilize the technique in shipbuilding and general repairs. Flux-cored technology is quicker than the other two methods.
The use of flux-cored arc welding also offers an essential aspect of versatility. With a semi-automatic process, the flux-cored technique is a more modern way of handling welding.
4. Plasma Arc Welding
You can also consider specializing in the plasma arc welding technique. This approach is quite similar to the gas tungsten arc welding. The arc in this method is formed between the electrodes by utilizing the temporary state of the gas furnace.
Most of the functionality of the Plasma arc welding approach depends on the ability by the plasma to transfer heat on the electric arc. With a constant intense heat, the metal then melts and fuses at the desired point. The temperature used is between 3000 and 7000 degrees, which may present a safety hazard to some extent.
Uses
The plasma arc welding technique is useful in most high-speed sheet welding projects. You may also thrive with this technique in areas such as keyhole welding and welding coated steels. The plasma arc welding method may also be used in the automotive and aerospace sectors when working on the bodywork.
You Have Unending Opportunities as a Welder
The demand for welding services will continue to grow steadily as the consumer market in the United States expands gradually. A career in welding will, therefore, be among the most lucrative blue-collar options in the future. Understanding these welding types and the welding types of jobs will give you leverage when it comes to information and career choices.
Explore our site further for more insightful content.
Comments are closed.