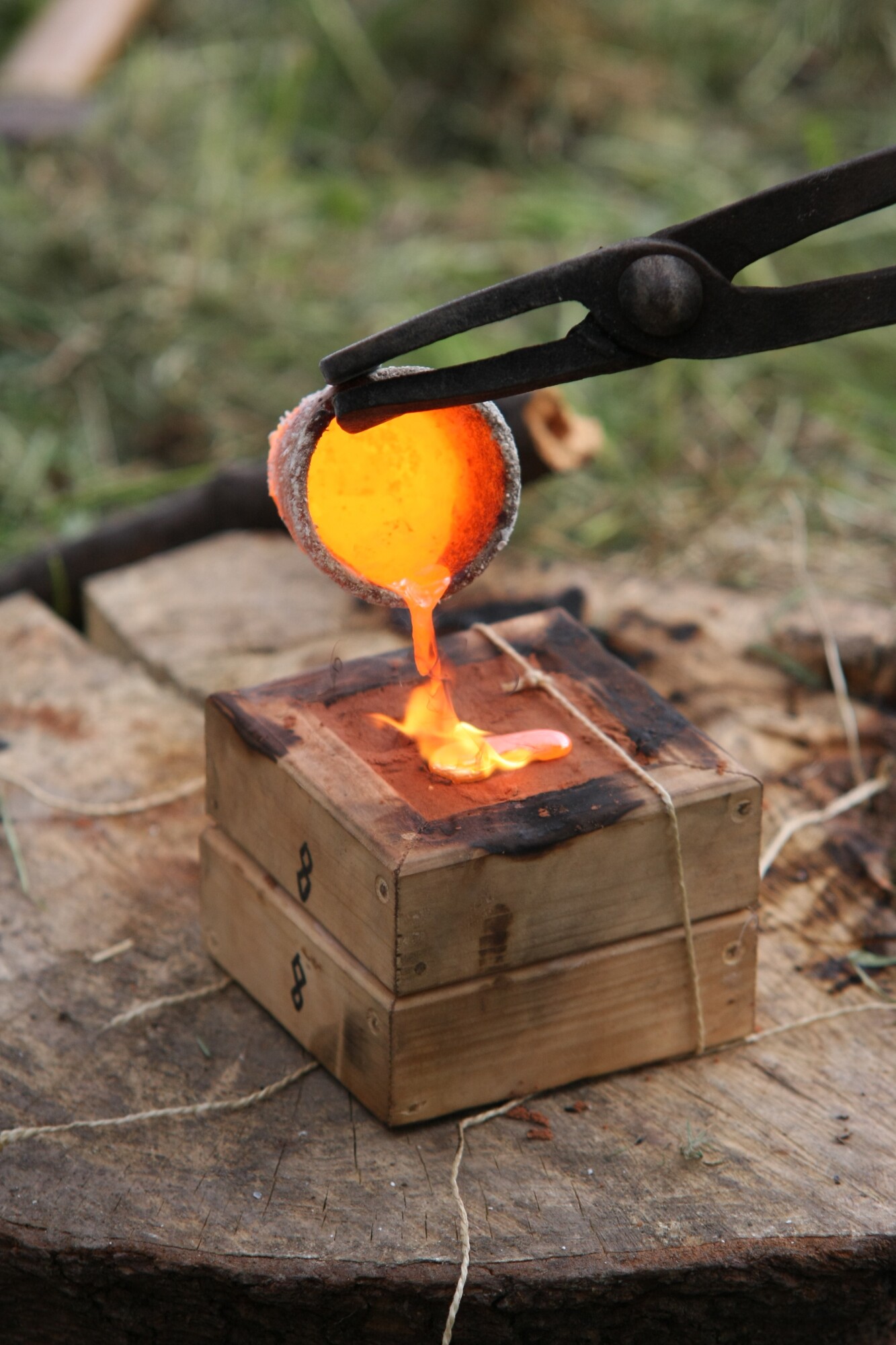
7 Benefits of Sand Casting
Ever wonder what went into the making of all of those intricate parts under the hood of your car? Probably not. But the process is quite interesting.
Your car’s cylinder heads, connecting rods, and transmission cases were all made using the process of sand casting.
Sand casting has been in existence for more than 5000 years. The process was first documented in 1540. However, it didn’t become a well-known process until the rapid expansion of the machine-building and automotive industries in the 20th century.
One million cars produced in 1924 by the Ford Motor Company accounted for one-third of the total sand casting production in the United States at the time. This increased demand resulted in new automation and mechanization methods for casting.
Contents
What is Casting?
Casting is the process that involves the pouring of liquified metal into a mold that is the shape of a specific part. It results in the metal solidifying in the shape of the mold. The object/part is then extracted from the mold.
The most common types of casting include:
- Sand Casting
- Investment Casting
- Plaster Casting
- Die Casting
All four techniques use similar steps with some variations in the casting process. The basic steps involved in the casting process include:
- Pattern Making
- Core Making
- Molding
- Melting and Pouring
- Cleaning
Sand casting is one of the best casting methods and accounts for 70% of all castings produced.
What is Sand Casting?
Sand casting is a versatile process that uses various metals to produce objects in different sizes, weights, and complex shapes. This casting technique uses a mold made from special sand. The mold is a negative impression that produces the desired component.
This makes the mold non-reusable as trying to keep the shape of it while removing the casting is difficult. It is a popular method for manufacturers because of its cost-effectiveness.
It also facilitates the production of large parts in a short time frame. It is ideal when melting specific metals at high temperatures such as nickel, titanium, and steel. Other casting metals can’t handle these metals due to the level of temperature required to melt them.
The advent of 3D printing introduced the use of 3D molds into the process which reduces the cost of sand casting by 75%.
Materials Used in Sand Casting
There are four basic materials used during the sand casting process.
Base Sand – used to make the sand in its pure state by combining it with a binding agent. The types of sand used include silica, olivine, chromite, zircon, and chamotte.
Binding Agent – the binding agent glues the sanding particles together. The type of binding agents used include clay and water, oil, resin, sodium, and silicate.
Additives – these improve the strength, cushioning, surface finish, and refractoriness of the mold.
Parting Compounds – facilitate the removal of the pattern from the mold.
Sand Casting Applications
There are sand casting applications in various industries but is heavily utilized in the aerospace and automotive industries to produce small parts. Heavy equipment manufacturing and the transport sector use over 50% of castings. Here are a few other applications of sand casting.
- Heavy Equipment – usually in construction, mining, and farming
- Transportation – in addition to the automotive and aerospace industries, casting is also used in railways and shipping
- Defense – used in military vehicles, munitions, artillery, storage, and supporting equipment
- Plant Machinery – utilized in the chemical, paper, petroleum, steel, sugar, and textile sectors as well as for thermal plants
- Machine Tools – used in machining, casting, forging, plastics molding, extrusion, and forming
- Electrical Machines – including motors, pumps, generators, and compressors
- Municipal Castings – more intricate parts such as joints, valves, pipes, and fittings
- Household – used in everyday appliances, furniture, fittings, and kitchen and gardening equipment
- Art Objects – furniture, lamp stands, sculptures, idols, and decorative items
Sand casting is an integral part of manufacturing and supports many industries. There are many components and enclosures produced using the sand casting process. You can learn more about them here.
Benefits of Sand Casting
The sand casting technique is responsible for the production of many important parts we use every day. It has become an integral part of many industries because it is a method that provides manufacturers with many benefits.
1. Cost-Effectiveness
The production costs in sand casting are low because tooling costs are low. Sand casting is an ideal choice for lower volumes of production. The expected usage quantity of the manufactured part will depend on the material selected for the pattern.
This is usually plastic, wood, or metal. Using machined molds for components expected to have lower usage over a longer period of time will make sand casting the more cost-effective option.
2. Metal Variety
Sand casting can be used to manufacture parts in all metals including those with a high-melting-point. Some other casting methods will melt if used. Because of this, some materials can only be produced using sand casting.
3. Versatility
Sand casting can create materials of all sizes and weights, from ounces to 200+ tons. Internal structures can be cast in place through the use of cores. Most sand castings need some machined surfaces.
This might be due to its pairing with other components or the innate tolerance limits of the process. Using this process can facilitate the creation of complex shapes and thin-wall sections.
4. No Quantity Limits
In addition to the versatility of the process, it also allows the production of large quantities. The tooling cost is so minimal that sand casting makes single-piece runs possible. Production of automotive components which require high-volume runs is also possible.
No matter the quantity, sand casting facilitates easy scaling. However, design elements and tolerance are still more important when selecting it as the preferred casting method.
5. Timeliness
The sand casting process can be faster than some other methods. However, post-casting processes such as machining are still considered when computing total lead times.
6. Accuracy
The process of sand casting has a high level of accuracy. This is why it can facilitate the production of objects of any size. It maintains this accuracy even for smaller elements. It also has a good surface finish.
7. Recyclable
It is possible to recycle sand casting scrap. There are a range of chemicals used in the binding agent, so if not discarded properly, sand casting scraps can leach into the environment. Some of the sand can also be reused in the casting process.
The Best Casting Method
Sand casting has been in existence for years. It played an integral part in the automotive industry with the manufacture of the Ford Model T. It is an established and proven method for the production of many items we use every day.
It is constantly adapted especially as a result of some of the new advances in technology. Get the latest news on this and other technological advancements in various industries at Donklephant.
Comments are closed.